https://jacobin.com/2023/09/
~~ recommended by emil karpo ~~
A key conflict in the United Auto Workers strike, which could begin at midnight tonight, is over the electric vehicle industry. The vast majority of EV plants are low-wage and nonunion despite being publicly subsidized — and the UAW is trying to fix that.
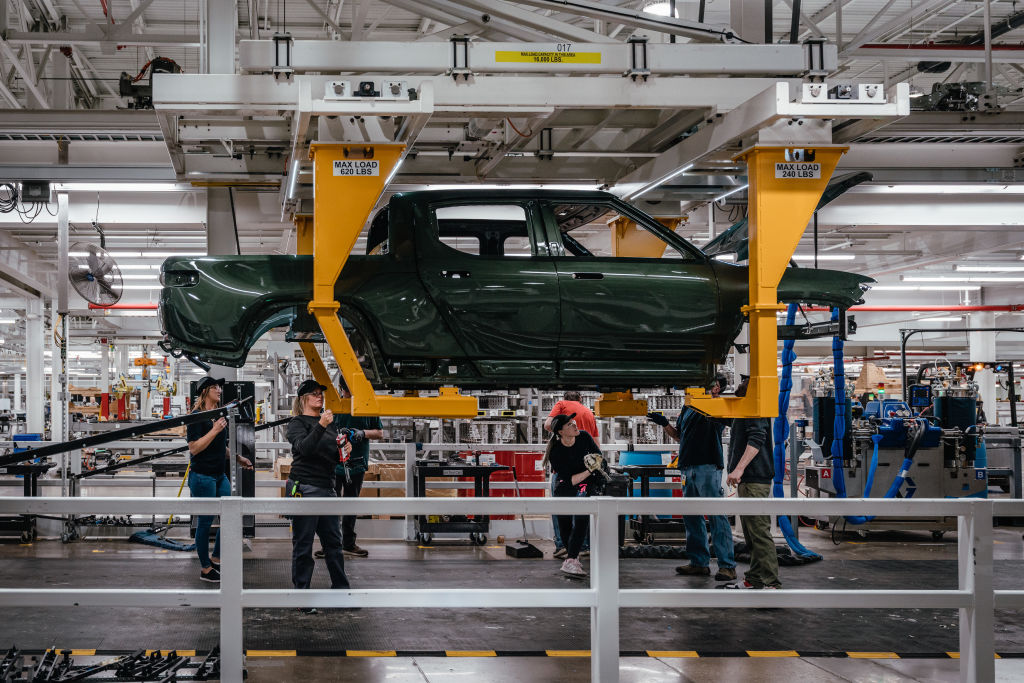
In the year since President Joe Biden signed the Inflation Reduction Act (IRA) in August 2022, its incentives and tax credits for electric vehicles (EV) have accelerated the United States’ burgeoning swath of battery plants. The EV industry will receive an estimated $220 billion by 2031, and customers purchasing a vehicle can pocket a tax credit ranging from $3,750 to $7,500. An increasing majority of battery components are to be produced and assembled domestically. While China remains the global leader in battery manufacturing, North America has emerged as the fastest-growing EV battery hub, surpassing Europe.
The IRA also extended additional manufacturing tax credits to the Internal Revenue Code. Companies are reimbursed 10 percent of the cost of producing renewable energy. The section grants a $35 credit for every kilowatt-hour of battery cell production and a $10 credit for those of modules. Various analysts estimate the ten-year tax credit may provide battery cell manufacturers with an extra $135-200 billion.
Amid high-stakes contract negotiations with the Big Three automakers, newly elected United Auto Workers (UAW) president Shawn Fain has criticized Biden’s packages for not tying public spending to worker protections. While the IRA includes prevailing wage standards and apprenticeship programs for the construction industry, it is silent on wages and working conditions in manufacturing. “The UAW supports and is ready for the transition to a clean auto industry,” Fain said in a late August statement. “But the EV transition must be a just transition that ensures auto workers have a place in the new economy.”
Shortly after the IRA’s first anniversary, the Biden administration announced an additional $15.5 billion to aid the auto companies’ transition. Biden’s nod to organized labor provided companies with a unionized workforce extra points on their application, but nothing more. While small compared to the largesse in the IRA, it reinforces the administration’s twin goals of drawing down the country’s reliance on China-based manufacturing and dramatically boosting the number of hybrid or fully electric vehicles available by 2030. As Secretary of Energy Jennifer Granholm put it, through linking the reduction of the country’s reliance on fossil fuels to the creation of a homegrown battery industry, the Biden administration aims at building a “global manufacturing powerhouse.”
For their part, auto companies and battery manufacturers are investing $100 billion in building new battery plants in the United States and Canada. Given that the technology was developed primarily by Chinese and South Korean companies, the Detroit Three are eager to partner with them. In most cases, the auto companies have set up new plants as joint ventures, conveniently bypassing their collective bargaining agreement with the UAW.
Elected as a reformer, Fain is making the demand for job security a central priority in negotiations. With the contract set to expire at midnight tonight, the Detroit Three have increased their offers but seem determined to keep a “temporary” or “supplemental” lower-wage/few-benefits layer of the workforce. A strike, beginning tomorrow, is almost certain.
The union would begin striking just a few plants across the three corporations. Everyone else would report for work, continue strike preparations, and be ready to walkout as needed.
Folding in battery workers into the “master agreement” would be a gigantic win as EV production revs up, but that isn’t on the table. However, the future of the workers in the United States’ blossoming, heavily subsidized EV sector is implicitly present. If the contract rolls back concessions, battery workers will flock to the UAW.
The First Plants to Open
The most common battery cell is the lithium ion. Cost efficient and easily stored, it is made from lithium, nickel, cobalt, and aluminum oxide. In addition to lithium deposits found in Bolivia, Chile, and Argentina, half a dozen states, including Nevada, California, Utah, and North Carolina contain lithium.
While battery cells comprise 25 to 30 percent of the total value of all EV parts and are the key component in the supply chain, the work is poorly paid. Workers earn an average of $17 to $21 an hour, have few benefits, and face dangerous working conditions. Government grants, loans, and tax credits contain no prevailing wage provision for workers making the product.
In the relatively new method of building battery cells for EVs, a cell consists of assembling three elements: a positive cathode, a negative anode, and an electrode — a liquid solution — that sits in between. Routine exposure to chemicals used for each component can cause respiratory tract, skin, or eye irritation; nausea; headaches; dizziness; and diarrhea. Acute exposure risks harm to one’s kidneys or reproductive system (including fetal damage) and can lead to germ cell mutations or cancer.
To minimize worker exposure, safety protocols must be established, meticulously followed, and updated. These include monitoring air quality, keeping certain chemicals away from heat, limiting contact with particular chemicals, and providing complete and transparent information about possible problems and finding alternatives.
After cells are placed into pouches, they are assembled into a dense network of battery cells at another facility — likewise, mostly nonunion.
The Reality of Battery Cell Production
Of the US battery plants in operation, the oldest is Tesla’s nonunion Gigafactory Nevada (2017). Since opening, the company has faced allegations of low pay, racial discrimination, labor law violations, and dangerous working conditions. Despite this history, Tesla’s investors expect to rake in a billion dollars in tax credits this year.
GM’s joint venture with LG Energy Solution, Ultium Cells Lordstown, Ohio, got off the ground in the summer of 2022. Estimating the cost of bringing the facility online at $2.3 billion, the company projected a work force of seventeen hundred. The starting wage was $16.50 an hour and was projected to top out at $20 after seven years. This year GM’s chief financial officer Paul Jacobson expects to collect $300 billion in tax credits.
On top of providing poor pay, the company has had serious safety issues. The latest incident, on August 23, was a n-Methylpyrrolidone (NMP) spill. The Environmental Protection Agency defines NMP as “an unreasonable risk” to human health at nearly every stage of commercial or consumer use. Other troubling issues include infrequent monitoring of air quality, failure to provide showers, and lack of exit routes.
As a result, newly employed workers took action. Many quit, while others signed cards to have the UAW become their union. When the company refused to recognize the union through “card check,” workers filed for an election with the National Labor Relations Board. Held over two days in December 2022, the election resulted in a 710-16 vote for the UAW.
Last month, workers ratified an interim contract (895-16) that boosted entry wages to $20. Based on hours worked, this will result in backpay of $3,000-$7,000. Working conditions, including health and safety, are still being negotiated, but the UAW is demanding the safety measures that have been so central to the UAW national agreement. A UAW report, “High Risk and Low Pay,” documented cases of workers sickened by chemicals. The report outlines strong and enforceable protocols in the UAW’s national agreement, including the right of workers to walk off the job under unsafe conditions.
But without a union — the situation of the vast majority of EV workers — safety issues are only covered by the underfunded Occupational Safety and Health Administration (OSHA). The UAW report concludes:
There will be tens of thousands of workers in battery plants in the near future. Establishing best practices at these plants now will set a high bar throughout the industry. Workers across the supply chain, from mining and mineral processing through final assembly of EVs, will be dealing with many hazards similar to those faced by workers at Ultium in Lordstown. Ramping up EV production to reduce climate impacts must not result in spreading dangerous manufacturing practices to communities across the country. All EV workers deserve robust protections and a voice in making their jobs safer.
The Building Frenzy
For the time being, the construction boom continues in nonunion plants.
Ultium Cells LLC is building two other battery plants, in Spring Hill, Tennessee, and Lansing, Michigan, at a cost of $2.6 billion each. Both will employ seventeen hundred workers and produce pouch-style cell packets. GM has announced a fourth joint venture, this time with South Korea’s Samsung SDI, making both prismatic and cylindrical cell packets.
For its part, Ford created a joint venture (JV) with South Korea SK On. BlueOval SK is building two plants in Kentucky at a cost of $5.8 billion and hiring five thousand workers. A third plant will be put up in BlueOval City, next to where Ford assembles an electric truck. That facility is projected to have twenty-five hundred workers with a total $5.6 billion investment for the entire complex. Finally, at a cost of $1.34 billion, Ford is reconfiguring its Oakville, Canada, assembly plant to package battery cells from a Kentucky plant.
The three US plants received a $9.2 billion loan from the Department of Energy, the largest loan a federal agency has approved to date for battery manufacture. The deal provides superior repayment terms, including debt forgiveness if the project doesn’t pan out. But there were no provisions for workers.
Things are slightly better in Marshall, Michigan, where Ford is planning on constructing a $3.5 billion, twenty-five-hundred-worker lithium iron phosphate plant, contracting with Chinese battery maker CATL. Ford company hasn’t agreed to union representation, but has said it would recognize the union through a card check process. In addition to federal grants and credits, the state of Michigan provided $36 million to get the site ready, $300 million to acquire the land and cut trees, another $330 million to develop roads and other necessary infrastructure; a $210 million grant; and a fifteen-year tax abatement that amounts to an estimated value of $772 million. Other states are ponying up money for the EV plants in their areas.
Nonunion companies are also getting in on the EV facility boomlet. Tesla plans to expand to a lithium refinery in Texas and produce battery cells, packs, and modules in California and Texas. Other companies investing in battery plants include BMW (South Carolina), Honda (Ohio), Hyundai (Georgia), Mercedes-Benz (Alabama), Toyota (North Carolina), Volkswagen (Ontario, Canada), and Volvo (South Carolina).
A variety of battery manufacturers are building new facilities, too. These include the Japanese company AESC (Tennessee, Kentucky, and South Carolina), the Chinese-owned Gotion (Michigan), South Korea’s LG Energy Solution (Arizona and Michigan) the start-up Our Next Energy (Michigan), Japanese-owned Panasonic (Kansas), South Korean SK Battery America (Georgia), and Redwood Materials, a recycling company (Nevada and South Carolina).
“No Concessions”
Past UAW officials did not address the coming restructuring of the auto industry, so the union is years late in developing a militant response. President Fain notes that over the last twenty years, sixty-five auto plants have closed and several parts plants have been sold off. Meanwhile, in the last decade alone, the Detroit Three enjoyed a quarter of a trillion dollars in profit. CEO compensation packages have exploded as the wages of autoworkers and the pensions of retirees stagnated.
The union insists that it makes no difference whether one works in a parts plant, an assembly facility, or a new battery plant — the right to a good-paying job, safe working conditions, and a life outside of work is essential. For its part, Stallantis insists on maintaining divisions — such as Mopar — where workers receive substandard pay. GM has that same demand for those who work for its subsidiaries, such as GM Components Holdings (GMCH) and GM Customer Care and After Sales (CCA).
The new leadership’s eagerness to galvanize membership for a “No Concessions” contract has meant organizing for a potential strike. They have adapted several methods developed by Teamsters for a Democratic Union: trainings on how to gather coworkers together to discuss contract demands, wearing red union T-shirts on Wednesdays, practice picketing, and where possible, strike preparation committees in the locals.
Most recently, the UAW held a Zoom training on how to talk to the media. This is a sharp contrast to the previous leadership’s “no comment” to reporters during negotiations. This, plus Fain’s weekly updates over Zoom and appearances at rallies, has kept members abreast of the negotiations. In those locals where the Administration Caucus (which ruled the union for decades) is telling members such strike preparation and militancy is harmful, members have tools to organize around this roadblock. But many local leaders, seeing members’ enthusiasm, have joined the campaign. The energy is contagious.
The old leadership failed to reverse the givebacks and proved incapable of organizing even one foreign auto “transplant.” Now the growth of joint venture EV plants has complicated the task. The new UAW strategy is to obtain a “No Concessions” contract with an eye toward moving on to organize nonunion plants. It has called on members to model themselves after the sit-down strikers of the ’30s and launch a Stand Up Strike midnight September 14.
Only such a militant union with innovative tactics and a commitment to move mountains will be capable of inspiring EV batter
No comments:
Post a Comment